Brick-Insulated Chamber Furnaces for Cooling/Relieving Stresses in Glass
Due to the five-sided heating and a special arrangement of the heating elements, the furnaces ensure good temperature uniformity.

Funkcja i wyposażenie
The chamber furnaces to 900 °C are ideally suited for cooling and relieving stresses in glass. Other applications include sterilizing glass components after they have been cleaned and burning in coatings. Due to the five-sided heating and a special arrangement of the heating elements, the furnaces ensure good temperature uniformity. With an extensive range of additional equipment, these chamber furnaces can be adapted to suit many different process requirements.
- Tmax 900 °C
- Dual shell housing made of textured stainless steel sheets with additional fan cooling for low surface temperature
- Five-side heating provide for good temperature uniformity
- Heating elements on support tubes provide for free heat radiation and long service life
- Multi-layer insulation consisting of lightweight refractory bricks and backed by special fiber insulation
- Exclusive use of insulation materials without categorization according to EC Regulation No 1272/2008 (CLP). This explicitly means that alumino silicate wool, also known as “refractory ceramic fiber” (RCF), which is classified and possibly carcinogenic, is not used.
- Self-supporting and long-life ceiling construction, with bricks laid in arched construction
- Bottom heating protected by SiC tiles with an even stacking base
- Semi-automatic air inlet flap for chamber kilns up to 300 liters
- Infinitely adjustable, manual air inlet from 360 liters
- Exhaust air opening in the lid, including connection for an exhaust air tube (80 mm diameter) up to 300 liters
- Motorized exhaust air flap in the top of the furnace for optimum ventilation of the furnace chamber and for rapid cooling at low temperatures from 300 liters
- Frame included for furnaces up to 660 liters
- Defined application within the constraints of the operating instructions
- NTLog Basic for Nabertherm controller: recording of process data with USB-flash drive
- Controller mounted on furnace door and removable for comfortable operation
- Controller with touch operation P570 (50 programs with each 40 segments)
Dodatkowe wyposażenie
- Automatic control of the air inlet flap (up to 300 liters)
- Motorized exhaust air flap for optimum ventilation of the furnace chamber and for rapid cooling at low temperatures (up to 300 liters, included from 360 liters)
- Cooling system, including P570 Controller, to speed up furnace cooling with a fan and specified temperature gradients or a fixed volume of fresh air. Both operating modes can be activated for different segments, using an extra function of the controller.
- Protective gas connection for purging the furnace with non-flammable protective or reaction gases
- Automatic gas supply system for nitrogen or argon
- Multi-zone control for optimal temperature uniformity in the work space
- Over-temperature limiter with adjustable cutout temperature as temperature limiter to protect the furnace and load
- Metal charging trolley with inserts for Tmax 550 °C or Tmax 800 °C
- Process control and documentation via VCD software package for monitoring, documentation and control
Specyfikacja techniczna
Model | Tmax | Inner dimensions in mm | Volume | Outer dimensions1 in mm | Heating power | Electrical | Weight | ||||
---|---|---|---|---|---|---|---|---|---|---|---|
°C | w | d | h | in l | W | D | H | in kW2 | connection | in kg | |
N 100/G | 900 | 400 | 530 | 460 | 100 | 720 | 1130 | 1440 | 7 | 3-phase | 275 |
N 150/G | 900 | 450 | 530 | 590 | 150 | 770 | 1130 | 1570 | 9 | 3-phase | 320 |
N 200/G | 900 | 470 | 530 | 780 | 200 | 790 | 1130 | 1760 | 11 | 3-phase | 375 |
N 200/GS | 900 | 400 | 1000 | 500 | 200 | 795 | 1710 | 1605 | 16 | 3-phase | 300 |
N 250/GS | 900 | 500 | 1000 | 500 | 250 | 895 | 1710 | 1605 | 18 | 3-phase | 370 |
N 300/G | 900 | 550 | 700 | 780 | 300 | 870 | 1300 | 1760 | 15 | 3-phase | 450 |
N 360/GS | 900 | 600 | 1000 | 600 | 360 | 995 | 1710 | 1705 | 20 | 3-phase | 500 |
N 440/G | 900 | 600 | 750 | 1000 | 440 | 1000 | 1410 | 1830 | 20 | 3-phase | 820 |
N 500/GS | 900 | 600 | 1400 | 600 | 500 | 995 | 2110 | 1705 | 22 | 3-phase | 1000 |
N 660/G | 900 | 600 | 1100 | 1000 | 660 | 1000 | 1750 | 1830 | 26 | 3-phase | 950 |
N 1000/G | 900 | 800 | 1000 | 1250 | 1000 | 1390 | 1760 | 2000 | 40 | 3-phase | 1680 |
N 1500/G | 900 | 900 | 1200 | 1400 | 1500 | 1490 | 1960 | 2150 | 57 | 3-phase | 2300 |
N 2200/G | 900 | 1000 | 1400 | 1600 | 2200 | 1590 | 2160 | 2350 | 75 | 3-phase | 2800 |
1External dimensions vary when furnace is equipped with additional equipment. Dimensions on request. |
Charging trolley | Trolley dimensions in mm | Insert dimensions in mm | Removable rails | |||||
---|---|---|---|---|---|---|---|---|
for model3 | W | D | H | W | D | H | Quantity | Distance in mm |
N 100/G | 370 | 505 | 410 | 315 | 470 | 22 | 12 | 30 |
N 150/G | 430 | 505 | 540 | 375 | 470 | 22 | 12 | 40 |
N 200/G | 450 | 505 | 730 | 395 | 470 | 22 | 17 | 40 |
N 300/G | 530 | 675 | 730 | 478 | 640 | 22 | 17 | 40 |
3Charging trolley for larger models available as a special design |
Zapytanie ofertowe
Dalsze produkty
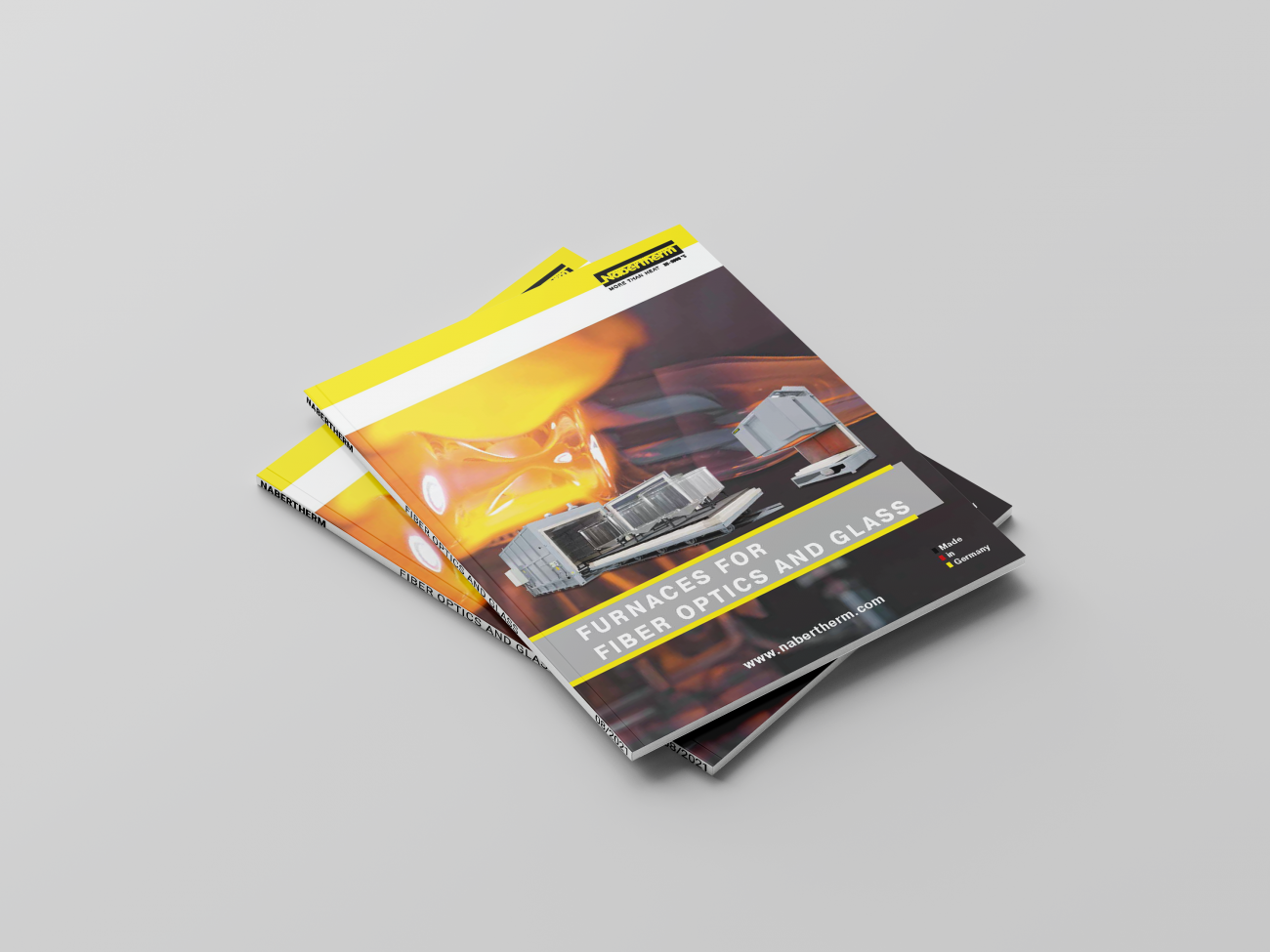
Katalogu
Kompletny przegląd naszej szerokiej oferty pieców z wysuwnym trzonem, pieców kołpakowych, pieców do topienia szkła i innych modeli do obróbki szkła można znaleźć w naszym katalogu „Technika światłowodowa / Szkło”.