Piece szybowe opadowe/pionowe instalacje do obróbki cieplnej
Piece szybowe opadowe idealnie nadają się do wyżarzania rozpuszczającego, hartowania i sztucznego starzenia stopów aluminium w jednym piecu.
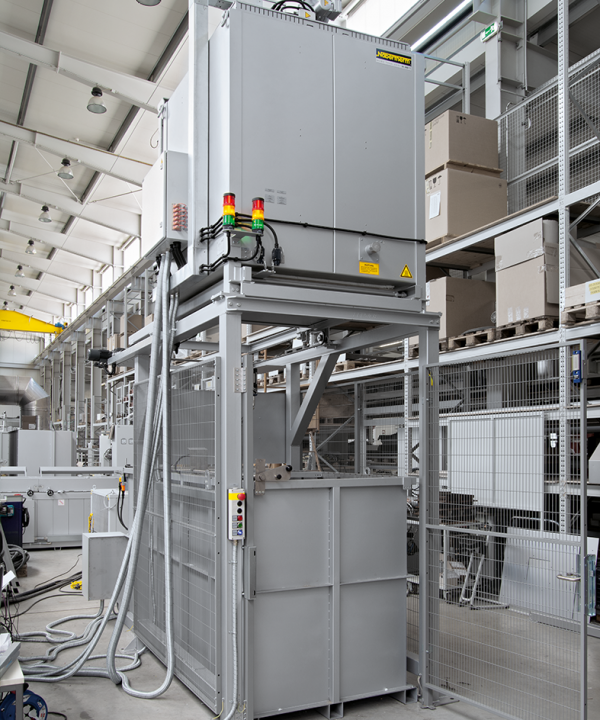
Funkcja i wyposażenie
Drop-bottom furnaces are used for solution annealing and subsequent rapid quenching of aluminum alloys. In particular, with thin-walled aluminum components, quench delay times of just five seconds from when the door begins to open until complete immersion in the quench tank are possible depending on the plant concept and size. Generally, these requirements can be met only with this furnace design. The drop-bottom furnace stands on a base so that a quench tank can be positioned directly below the furnace. For the quenching process, the door moves horizontally to the side and a basket containing the components is lowered into the quench tank by means of a lifting device that is integrated in the furnace. The conveying technology can be controlled automatically or semi-automatically.
Because of the broad working temperature range, drop-bottom furnace plants allow complete T6-heat treatments, consisting of solution annealing, quenching, and artificial aging in just one furnace. If required, the artificial aging can also take place in a separate furnace outside the system.
Standard Equipment Drop-Bottom Furnace Plants
- Installed on a frame
- Working temperature range between 80 °C and 600 °C
- Electrically heated
- Air flow, depending on space conditions and charge geometry, horizontal or vertical
- Over-temperature limiter with adjustable cutout temperature as temperature limiter to protect the furnace and load
- Exclusive use of insulation materials without categorization according to EC Regulation No 1272/2008 (CLP). This explicitly means that alumino silicate wool, also known as “refractory ceramic fiber” (RCF), which is classified and possibly carcinogenic, is not used.
- Defined application within the constraints of the operating instructions
- Siemens PLC controls with touchpanel as operating interface
Standard Design Variant A
This is the least expensive and most space-saving variant and offers the following features:
Loading
- The charge is loaded onto the charge carrier, which is above the quench tank in the plant, with a forklift truck
- Fastest quench delay time in seven seconds
Quench Tank
- Fixed, below the furnace
- Tank with circulation, fresh water cooling, level control and temperature monitoring
Standard Design Variant B
Equipment, see variant A, but lower construction height with movable platform bogie with loading space and water tank.
Loading
- The charge is loaded onto a holding position which is on a bogie on rails
- The bogie is then moved beneath the furnace and the furnace loading system picks up the charge carrier
- Fastest quench delay time in five seconds
Quench Tank
- The quench tank and basket position are installed together on a bogie
- After loading is complete, the bogie is moved beneath the furnace. The charge is lowered automatically into the tank for quenching.
- Due to the low height, this plant concept allows the fastest quench times of just five seconds
Standard Design Variant C
Equipment, see variant A, but lower construction height with water tank built into the floor.
Loading
- The charge is loaded onto a holding position which is on a bogie on rails
- The bogie is then moved beneath the furnace and the furnace loading system picks up the charge carrier
- When the charge is in the furnace, the bogie is moved again to the position beside the furnace
- Fastest quench delay time in seven seconds
Quench Tank
- The quench tank is built into the floor
Dodatkowe wyposażenie
Extension Options for all Variants
- Automatic mode
- Additional furnaces for alternating operating with several baskets
- Additional parking positions
- Controlled cooling of the furnace with fresh-air fan
- Charging baskets
- PC-based software, Nabertherm Control Center, for visualization, control and process documentation
- Working temperature can be extended to 650 °C
- Direct or indirect gas heating as alternative to electric heating
- Compliance with relevant aviation and automotive standards, such as AMS2750H, AMS2770/2771 or CQI-9 as an option
- Process control and documentation via VCD software package for monitoring, documentation and control
- Customized extensions
Specyfikacja techniczna
Model | Tmax | Inner dimensions in mm | Max. charging weight | Height with quench tank on the floor | Height with quench tank on a bogie | Heating power | ||
---|---|---|---|---|---|---|---|---|
°C | w | d | h | in kg | in mm | in mm | in kW1 | |
FS 1200/60A | 600 | 600 | 600 | 1000 | 150 | 4870 | 4200 | 36 |
FS 4000/60HA | 600 | 1100 | 1100 | 1100 | 350 | 7300 | 5700 | 96 |
FS 5600/60A | 600 | 1400 | 1400 | 1100 | 1200 | 7300 | 5700 | 120 |
1Depending on the furnace design, connected load might be higher |
Zapytanie ofertowe
Dalsze produkty

Katalogu
Kompletny przegląd naszej szerokiej oferty pieców i instalacji do obróbki cieplnej prowadzonej w atmosferze powietrznej można znaleźć w naszym katalogu „Technologia procesów termicznych 1”.