Compact Chamber Furnaces LH .. DB for Debinding and Sintering in Additive Manufacturing
As a hybrid furnace solution, the system can be converted to the operation under protective gas atmosphere with the optional protective gas box.

Function and equipment
The chamber furnaces of the model series LH .. DB set new standards for debinding and sintering conventionally manufactured ceramic parts in laboratory scale as well as for thermal post-processing of 3D printed components. Due to the compact design, controllers, controls and switchgear are integrated directly in the furnace housing. After connecting to the power supply, the furnace is immediately ready for use.
The heat treatment is not limited to processes in air. As a hybrid furnace solution, the system can be converted to the operation under protective gas atmosphere with the optional protective gas box. This allows 3D printed components made of metal or other materials requiring an inert atmosphere to be debinded up to 600 °C. A subsequent heat treatment under non-flammable process gas is possible up to 1100 °C.
Safe operation of the furnace is ensured by the DB debinding package. For processes under air, fresh air dilutes the exhaust gases evaporating from the charge to prevent a combustible atmosphere inside the furnace. During inert debinding, the safety system monitors the volume flow of the non-flammable process gas ensuring reliable flushing of the protective gas box. Regardless of the operation mode during debinding, the fresh air supplied to the furnace chamber is preheated. This improves heat transfer to the charge and ensures a uniform debinding.
- Tmax 1300 °C
- Dual shell housing made of textured stainless steel sheets with additional fan cooling for low surface temperature
- Heating elements on support tubes ensure free heat radiation and a long service life
- Multi-layer insulation consisting of light refractory bricks backed by special insulation
- Exclusive use of insulation materials without categorization according to EC Regulation No 1272/2008 (CLP). This explicitly means that alumino silicate wool, also known as “refractory ceramic fiber” (RCF), which is classified and possibly carcinogenic, is not used.
- Debinding package DB
- Fresh air fan and air preheater
- Exhaust gas and exhaust air removed via one outlet with a motor-driven flap into an exhaust hood
- Automatic gas supply system for flushing the furnace chamber or the optional protective gas box with non-flammable process gases
- Defined application within the constraints of the operating instructions
- Controller with touch operation P570 (50 programs with each 40 segments)
Additional equipment
- Protective gas box for debinding under non-flammable process gases up to 600 °C and subsequent heat treatment up to 1100 °C
Technical specifications
Model | Tmax | Inner dimensions in mm | Work space in optional | Volume | Outer dimensions1 in mm | Connected load2 | Electrical | Weight | ||||||
---|---|---|---|---|---|---|---|---|---|---|---|---|---|---|
in °C | w | d | h | w | d | h | in l | W | D | H | in kW | connection | in kg | |
LH 120/13 DB | 1300 | 500 | 500 | 500 | 300 | 300 | 300 | 120 | 930 | 1220 | 2090 | 24.5 | 3-phase | 410 |
LH 216/13 DB | 1300 | 600 | 600 | 600 | 400 | 400 | 400 | 216 | 1030 | 1320 | 2190 | 32.0 | 3-phase | 600 |
1External dimensions vary when furnace is equipped with additional equipment. Dimensions on request. |
Request for quotation
Further products
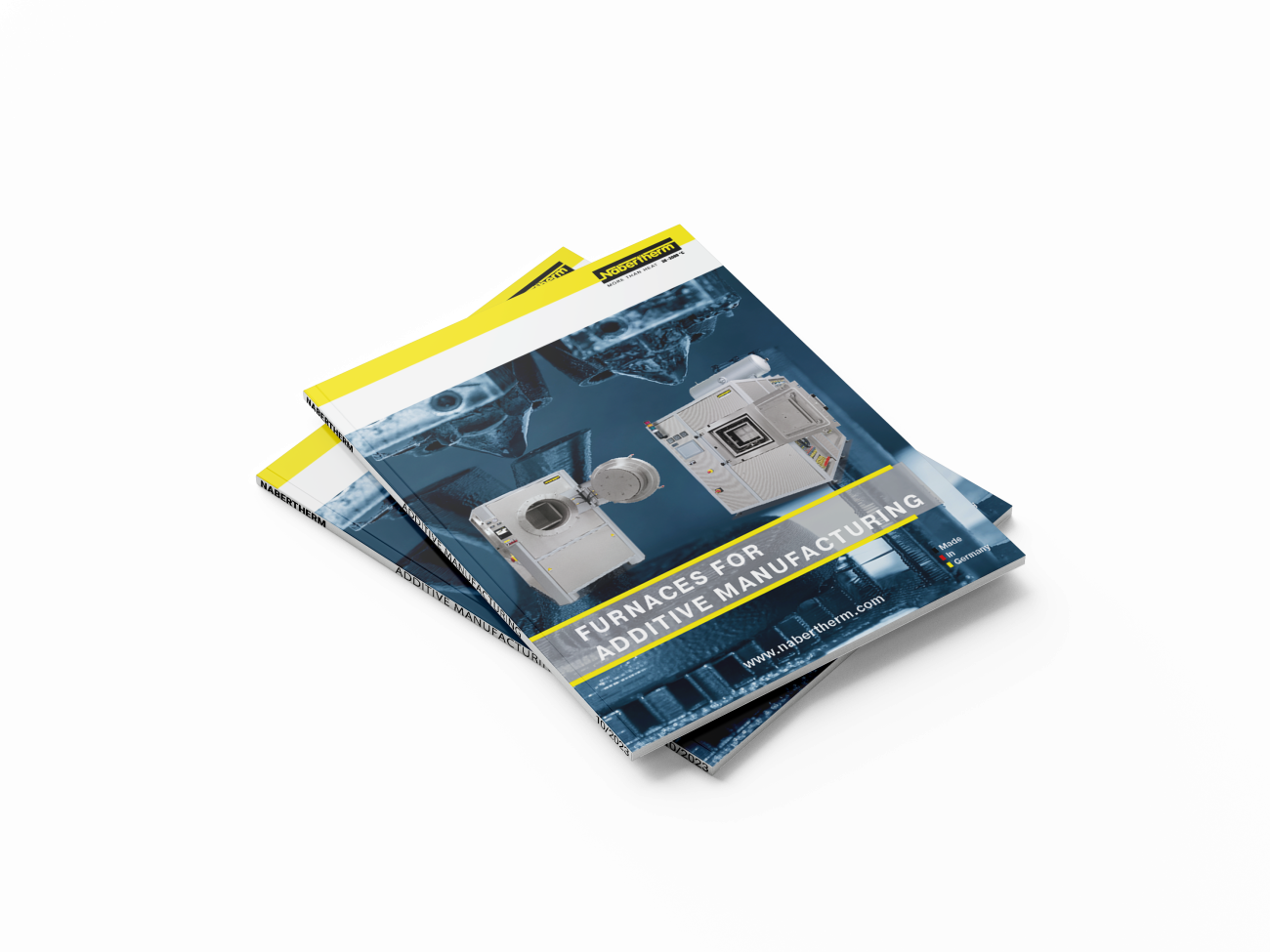
Catalog
A complete overview of our extensive range of furnace concepts for heat treatment after 3D printing can be found in our catalog “Additive Manufacturing”.