High-Temperature Furnaces with Molybdenum Disilicide Heating Elements with Fiber Insulation up to 1800 °C
Oustanding temperature uniformity and practical details set very high quality benchmarks.
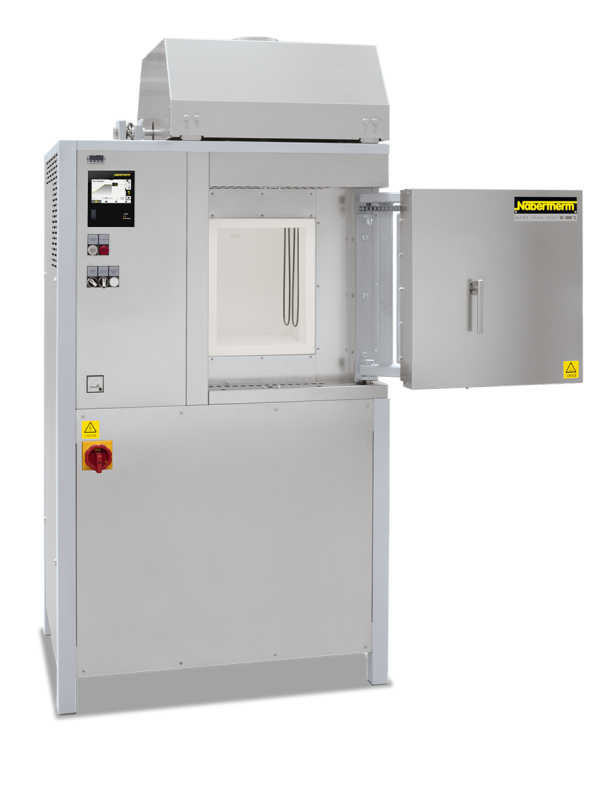
Function and equipment
High-temperature furnace HT 29/17
High temperature chamber furnace HT 450/16 with two locking devices per door
High-temperature furnace HT 160/17 with gas supply system
High-temperature furnace HT 64/17 with PLC controls and additional options
Automatic gas supply system with solenoid valve and rotameter
Two-door design for high-temperature furnaces > HT 276/..
Reinforced floor as protection for bottom insulation for high-temperature furnace HT 16/16 and higher
Cooled inspection glass made out of saphire glass (left at working temperature, right at room temperature)
Due to their solid construction and compact stand-alone design, these high-temperature furnaces are perfect for processes in the laboratory where the highest precision is needed. Oustanding temperature uniformity and practical details set unbeatable quality benchmarks. For configuration for your processes, these furnaces can be extended with extras from our extensive option list.
- Tmax 1600 °C, 1750 °C, or 1800 °C
- Recommended working temperature 1750 °C (for models HT ../18), increased wear and tear must be expected in case of working at higher temperatures
- Dual shell housing with fan cooling for low shell temperatures
- Heating from both sides via molybdenum disilicide heating elements
- High-quality fiber insulation backed by special insulation
- Long-life roof insulation with special suspension
- Temperature uniformity at 1450 °C up to +/− 6 °C according to DIN 17052-1
- Exclusive use of insulation materials without categorization according to EC Regulation No. 1272/2008 (CLP)
- Chain-guided parallel swivel door for precise opening and closing of the door
- Two-door design (front/back) for high-temperature furnaces from HT 276/..
- Labyrinth sealing ensures the least possible temperature loss in the door area
- Reinforced floor as protection for bottom insulation as standard from models HT 16/16 upwards (distributed load 5 kg/dm2)
- Vapor vent in the furnace roof with motorized exhaust air flap, controlled via the extra function of the controller
- Stainless steel exhaust hood as interface to customer’s exhaust system
- Defined application within the constraints of the operating instructions
- NTLog Basic for Nabertherm controller: recording of process data with USB-flash drive
- Controller with touch operation P570 (50 programs with each 40 segments)
Additional equipment
Additional equipment
- Uncontrolled or controlled cooling system with frequency-controlled cooling fan and motorized exhaust air flap
- Furnace in DB design featuring fresh air preheating, exhaust gas ventilation and an extensive safety package for debinding and sintering in one process, i. e. without transfering the material from the debinding furnace to the sintering furnace
- Thermocouple inlet with screw cap
- Thermocouple for the heating control with calibration certificate
- Protective gas connection to purge with non-flammable process gases (not completely gas-tight)
- Automatic gas supply system with solenoid valve and rotameter, controlled by the extra function of the controller
- Refractory brick floor insulation for a higher floor load (Tmax 1700 °C)
- Lift door
- Automatic door lock incl. door contact switch
- Heating elements protected against mechanical damage
- Special heating element qualities e. g. for zircon oxide applications
- Ethernet interface
- Process control and documentation via VCD software package for monitoring, documentation and control
Technical specifications
Model | Tmax | Inner dimensions in mm | Volume | Outer dimensions1 in mm | Connected | Electrical | Weight | ||||
---|---|---|---|---|---|---|---|---|---|---|---|
°C | w | d | h | in l | W | D | H | load kW | connection | in kg | |
HT 08/16 | 1600 | 150 | 300 | 150 | 8 | 740 | 640 | 1755 | 8.5 | 3-phase2 | 215 |
HT 16/16 | 1600 | 200 | 300 | 260 | 16 | 820 | 690 | 1860 | 12.5 | 3-phase2 | 300 |
HT 29/16 | 1600 | 275 | 300 | 350 | 29 | 985 | 740 | 1990 | 9.8 | 3-phase2 | 350 |
HT 40/16 | 1600 | 300 | 350 | 350 | 40 | 1010 | 800 | 1990 | 12.5 | 3-phase | 420 |
HT 64/16 | 1600 | 400 | 400 | 400 | 64 | 1140 | 890 | 2040 | 18.5 | 3-phase | 555 |
HT 128/16 | 1600 | 400 | 800 | 400 | 128 | 1140 | 1280 | 2040 | 26.5 | 3-phase | 820 |
HT 160/16 | 1600 | 500 | 550 | 550 | 160 | 1250 | 1040 | 2260 | 21.5 | 3-phase | 760 |
HT 276/16 | 1600 | 500 | 1000 | 550 | 276 | 1340 | 1600 | 2290 | 36.5 | 3-phase | 1270 |
HT 450/16 | 1600 | 500 | 1150 | 780 | 450 | 1380 | 1820 | 2570 | 65.0 | 3-phase | 1570 |
HT 08/17 | 1750 | 150 | 300 | 150 | 8 | 740 | 640 | 1755 | 8.5 | 3-phase2 | 215 |
HT 16/17 | 1750 | 200 | 300 | 260 | 16 | 820 | 690 | 1860 | 12.5 | 3-phase2 | 300 |
HT 29/17 | 1750 | 275 | 300 | 350 | 29 | 985 | 740 | 1990 | 9.8 | 3-phase2 | 350 |
HT 40/17 | 1750 | 300 | 350 | 350 | 40 | 1010 | 800 | 1990 | 12.5 | 3-phase | 420 |
HT 64/17 | 1750 | 400 | 400 | 400 | 64 | 1140 | 890 | 2040 | 18.5 | 3-phase | 555 |
HT 128/17 | 1750 | 400 | 800 | 400 | 128 | 1140 | 1280 | 2040 | 26.5 | 3-phase | 820 |
HT 160/17 | 1750 | 500 | 550 | 550 | 160 | 1250 | 1040 | 2260 | 21.5 | 3-phase | 760 |
HT 276/17 | 1750 | 500 | 1000 | 550 | 276 | 1340 | 1600 | 2290 | 36.5 | 3-phase | 1270 |
HT 450/17 | 1750 | 500 | 1150 | 780 | 450 | 1380 | 1820 | 2570 | 65.0 | 3-phase | 1570 |
HT 08/18 | 1800 | 150 | 300 | 150 | 8 | 740 | 640 | 1755 | 8.5 | 3-phase2 | 215 |
HT 16/18 | 1800 | 200 | 300 | 260 | 16 | 820 | 690 | 1860 | 12.5 | 3-phase2 | 300 |
HT 29/18 | 1800 | 275 | 300 | 350 | 29 | 985 | 740 | 1990 | 9.8 | 3-phase2 | 350 |
HT 40/18 | 1800 | 300 | 350 | 350 | 40 | 1010 | 800 | 1990 | 12.5 | 3-phase | 420 |
HT 64/18 | 1800 | 400 | 400 | 400 | 64 | 1140 | 890 | 2040 | 18.5 | 3-phase | 555 |
HT 128/18 | 1800 | 400 | 800 | 400 | 128 | 1140 | 1280 | 2040 | 26.5 | 3-phase | 820 |
HT 160/18 | 1800 | 500 | 550 | 550 | 160 | 1250 | 1040 | 2260 | 21.5 | 3-phase | 760 |
HT 276/18 | 1800 | 500 | 1000 | 550 | 276 | 1340 | 1600 | 2290 | 36.5 | 3-phase | 1270 |
HT 450/18 | 1800 | 500 | 1150 | 780 | 450 | 1380 | 1820 | 2570 | 65.0 | 3-phase | 1570 |
1External dimensions vary when furnace is equipped with additional equipment. Dimensions on request. 2Heating only between two phases |
Request for quotation
Archivo de vídeo
Further products
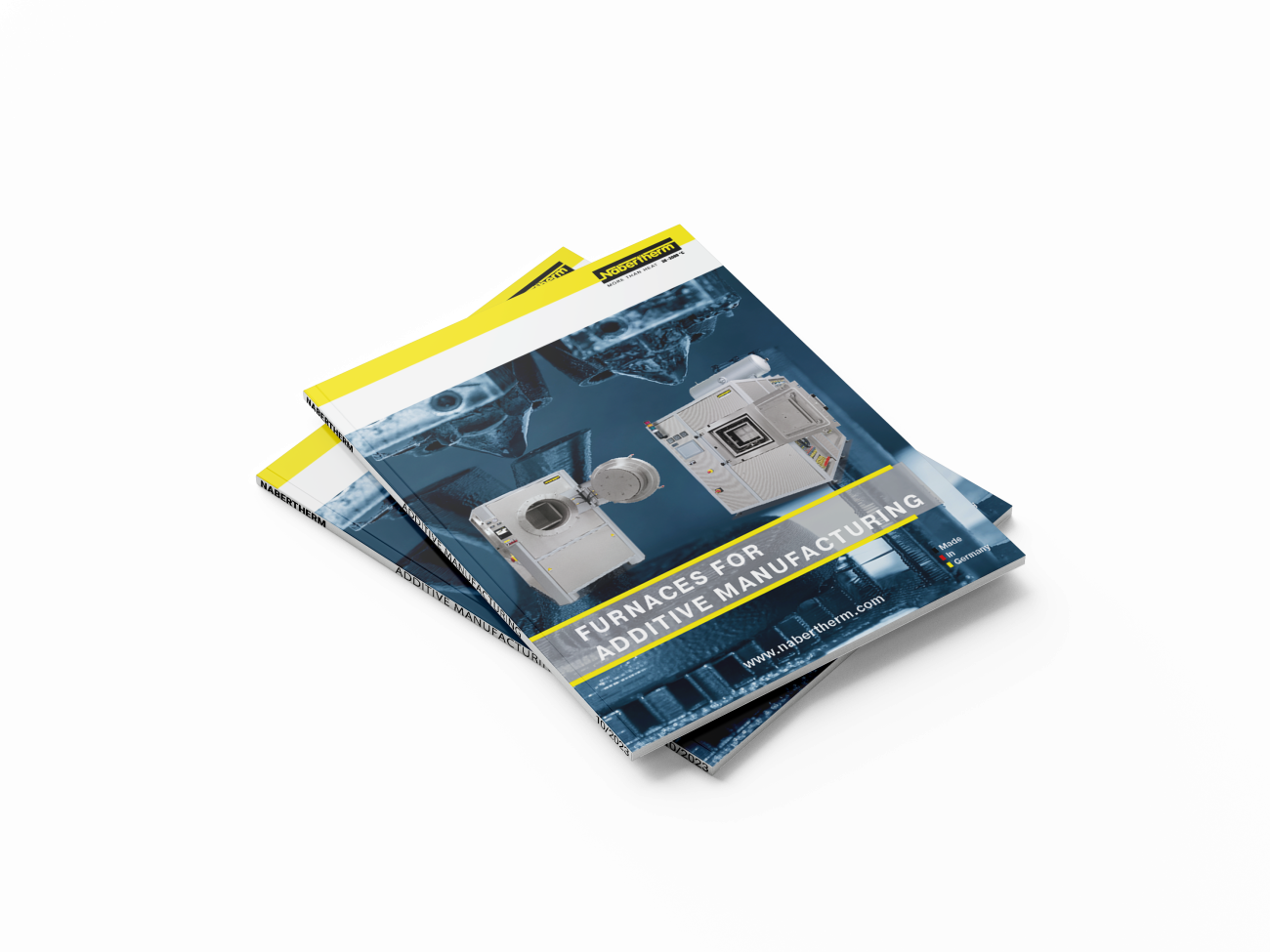
Catalog
A complete overview of our extensive range of furnace concepts for heat treatment after 3D printing can be found in our catalog “Additive Manufacturing”.