Chamber Ovens up to 260 °C
A wide range of accessories allow the chamber ovens to be modified to meet specific process requirements.

Function and equipment
Chamber oven KTR 6125
Chamber oven KTR 6250 with double doors in the front and in the back as well as guide-in tracks for use as sluice oven
Chamber oven KTR 1500 with charging cart
Charging cart with pull-out trays
Drive-in ramp
Pull-out shelves, running on rolls
The chamber ovens of the KTR range can be used for complex drying processes and heat treatment of charges to an application temperature of 260 °C. The high-performance air circulation enables optimum temperature uniformity throughout the work space. A wide range of accessories allow the chamber ovens to be modified to meet specific process requirements.
Standard Equipment
- Tmax 260 °C
- Electrically heated (via a heating register with integrated chrome steel heating elements) or gas-fired (direct or indirect gas-fired including injection of the hot air into the intake duct)
- Temperature uniformity up to +/− 3 °C according to DIN 17052-1 (for design wihout track cutouts)
- High-quality mineral wool insulation provides for outer temperatures of < 25 °C above room temperature
- Exclusive use of insulation materials without categorization according to EC Regulation No 1272/2008 (CLP). This explicitly means that alumino silicate wool, also known as “refractory ceramic fiber” (RCF), which is classified and possibly carcinogenic, is not used.
- High air exchange for fast drying processes
- Double-wing door for furnaces KTR 2300 and larger
- Over-temperature limiter with adjustable cutout temperature as temperature limiter to protect the furnace and load
- Controller with touch operation B500 (5 prgrams with each 4 segments)
- Defined application within the constraints of the operating instructions
- NTLog Basic for Nabertherm controller: recording of process data with USB-flash drive
Additional equipment
Additional Equipment
- Direct or indirect gas-fired
- Base frame to charge the oven via a charging forklift
- Additional door in the back for charging from both sides or to use the oven as lock between two rooms
- Fan system for faster cooling with manual or motorized control of the exhaust flaps
- Programmed opening and closing of exhaust air flaps
- Air circulation with speed control, recommendable for processes with light or sensitive charge
- Observation window and furnace chamber lighting
- Design for clean room heat treatment processes
- Rotating systems e. g. for tempering processes
- All KTR-models are also available with Tmax 300 °C
- Process control and documentation via VCD software package or Nabertherm Control Center (NCC) for monitoring, documentation and control
Technical specifications
Model | Tmax | Inner dimensions in mm | Volume | Outer dimensions2 in mm | Heating power | Electrical | ||||
---|---|---|---|---|---|---|---|---|---|---|
°C | w | d | h | in l | W | D | H | in kW1 | connection | |
KTR 1000 | 260 | 1000 | 1000 | 1000 | 1000 | 1815 | 1430 | 1890 | 18 | 3-phase |
KTR 1500 | 260 | 1000 | 1000 | 1500 | 1500 | 1815 | 1430 | 2390 | 18 | 3-phase |
KTR 2000 | 260 | 1100 | 1500 | 1200 | 2000 | 1915 | 1930 | 2090 | 18 | 3-phase |
KTR 2300 | 260 | 1250 | 1250 | 1500 | 2300 | 2115 | 1680 | 2515 | 27 | 3-phase |
KTR 3100 | 260 | 1250 | 1250 | 2000 | 3100 | 2115 | 1680 | 2960 | 27 | 3-phase |
KTR 3400 | 260 | 1500 | 1500 | 1500 | 3400 | 2445 | 1930 | 2460 | 45 | 3-phase |
KTR 4500 | 260 | 1500 | 1500 | 2000 | 4500 | 2445 | 1930 | 2960 | 45 | 3-phase |
KTR 4600 | 260 | 1750 | 1750 | 1500 | 4600 | 2695 | 2175 | 2480 | 45 | 3-phase |
KTR 6000 | 260 | 2000 | 2000 | 1500 | 6000 | 2945 | 2430 | 2460 | 54 | 3-phase |
KTR 6125 | 260 | 1750 | 1750 | 2000 | 6125 | 2695 | 2175 | 2980 | 45 | 3-phase |
KTR 6250 | 260 | 1250 | 2500 | 2000 | 6250 | 2195 | 3035 | 2960 | 54 | 3-phase |
KTR 8000 | 260 | 2000 | 2000 | 2000 | 8000 | 2945 | 2430 | 2960 | 54 | 3-phase |
KTR 9000 | 260 | 1500 | 3000 | 2000 | 9000 | 2565 | 3870 | 2920 | 72 | 3-phase |
KTR 12300 | 260 | 1750 | 3500 | 2000 | 12300 | 2695 | 4350 | 2980 | 90 | 3-phase |
KTR 13250 | 260 | 1250 | 5000 | 2000 | 13250 | 2195 | 6170 | 2960 | 108 | 3-phase |
KTR 16000 | 260 | 2000 | 4000 | 2000 | 16000 | 2945 | 4850 | 2960 | 108 | 3-phase |
KTR 21300 | 260 | 2650 | 3550 | 2300 | 21300 | 3675 | 4195 | 3380 | 108 | 3-phase |
KTR 22500 | 260 | 2000 | 4500 | 2500 | 22500 | 3015 | 5300 | 3550 | 108 | 3-phase |
1Depending on furnace design connected load might be higher 2External dimensions vary when furnace is equipped with additional equipment. Dimensions on request. |
Request for quotation
Archivo de vídeo
Archivo de vídeo
Archivo de vídeo
Further products
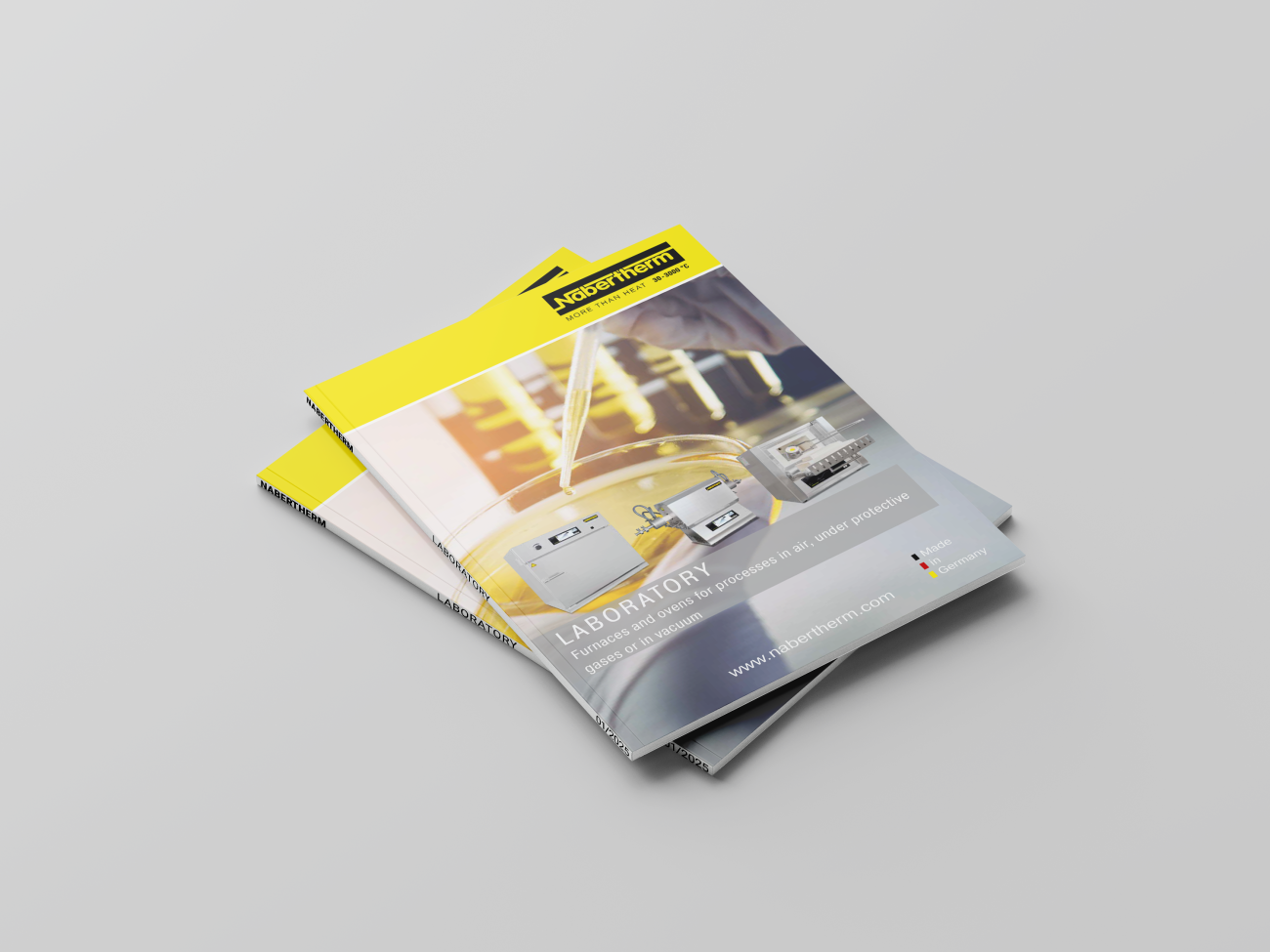
Catalog
A complete overview of our extensive range of furnaces, ovens and accessories for the laboratory can be found in our “Laboratory” catalog.