Paleniska i piece z technologią bezpieczeństwa zgodną z EN 1539
Norma europejska EN 1539 opisuje konstrukcje technologii bezpieczeństwa do palenisk i pieców, w których uwalniane i odparowywane są rozpuszczalniki lub inne substancje palne.
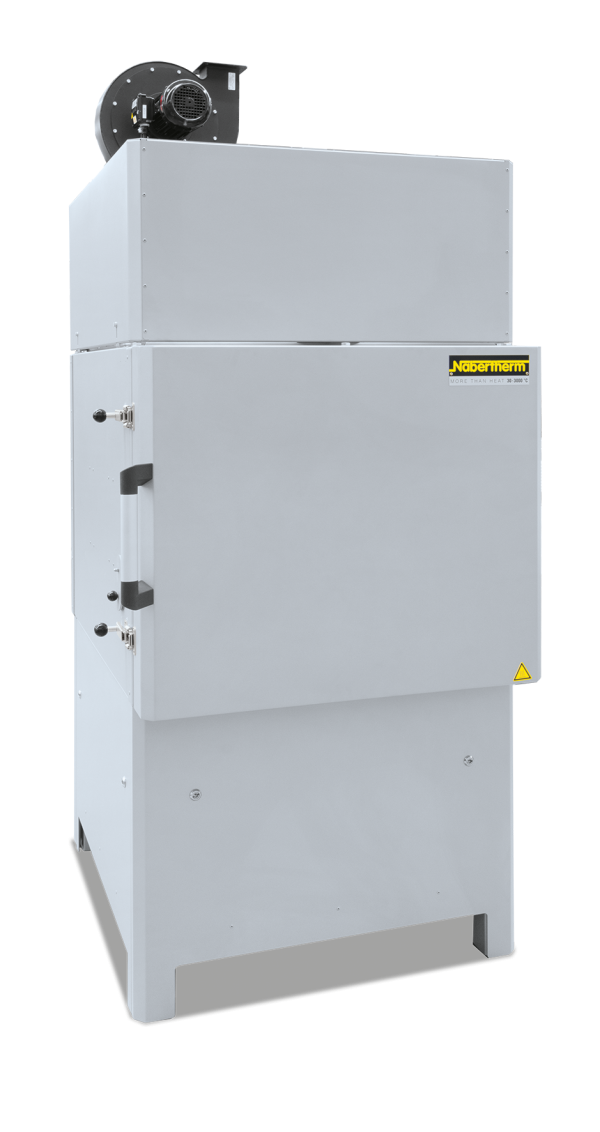
Paleniska i piece z technologią bezpieczeństwa zgodną z EN 1539
The safety technology of furnaces and ovens used for processes in which solvents or other flammable substances are released and vaporized relatively quickly is regulated throughout Europe in EN 1539.Typical applications are drying of mold varnishes, surface coatings, and impregnating resins. Users include the chemical industry as well as many other areas, such as the automotive, electric, plastics processing and metalworking industries
The safety concept relates to preventing the formation of explosive mixtures through continuous ventilation in the entire vapor space.
Implementation of the Standard Requirements
An exhaust gas fan ensures continuous ventilation in the oven or furnace. The safety function of the fan is monitored. The vapors occurring during heat treatment are extracted from the furnace chamber with the aid of the exhaust gas fan. The air exchange rate is ensured via a differential pressure system (differential pressure monitoring of the air circulation and the exhaust gas). If the system reports a fault, the furnace goes into malfunction mode and the heating is stopped. Underpressure ensures that the solvent is able to exit the furnace in a controlled manner. The interior of the furnace is completely welded and prevents solvent penetrating and accumulating in the insulation.
Nabertherm specifies the amount of solvent that can be introduced in relation to the working temperature and furnace model. The quantity of solvent is calculated in relation to the worst-case scenario; in other words, rapid evaporation of solvent on the largest possible surface area.
The standard also allows for exceptions where, with lower evaporation rates, larger volumes of solvent per charge may be introduced to the oven. Therefore, customers should always assess the process to comply with the permitted quantity of solvent.
When mold varnishes are being dried, the standard values can be increased by a factor of 10. If the customer's process involves drying impregnating resin (e.g. for transformers, motor windings, etc.), the maximum quantities of flammable materials calculated for rapid evaporation can be increased by a factor of 20. Depending on the process, customers must comply with the current standards.
The high rate of air exchange results in relatively high energy consumption. In EN 1539, it states that, when the main evaporation time has expired, the minimum volumetric flow rate of the exhaust air may be reduced to 25%. According to EN 1539, the main evaporation time is the time in which the main quantity of flammable substances is released. For ovens with safety technology, Nabertherm offers an additional control system to implement this energy saving option. Customers must set and acknowledge the end of the main evaporation time. When this time is reached, the system reduces the volumetric flow rate of the exhaust gas accordingly.
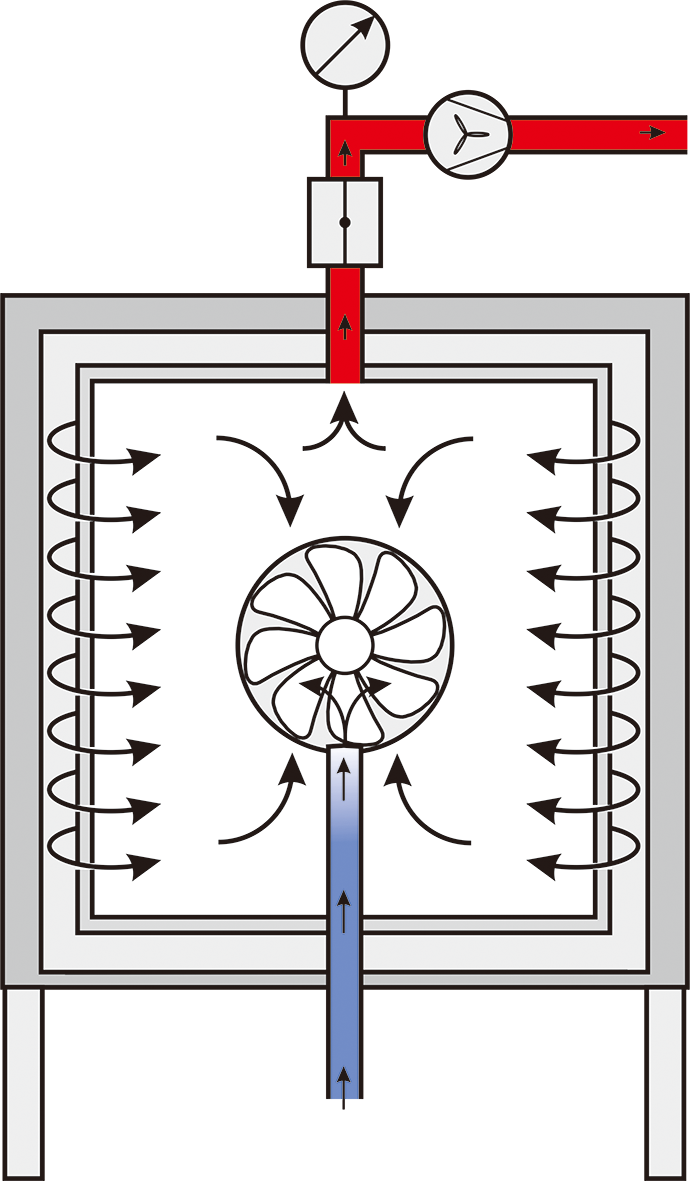