Rotary Tube Furnaces for Processes with Continuous Movement up to 1300 °C
Equipped with the optionally available closed feeding system, the rotary tube furnace can also be used for processes in a defined atmosphere or in a vacuum.

Function and equipment
The rotary tube furnaces of the RSRC series are particularly suitable for processes in which continuously running batch material is heated short-time. These rotary furnaces can be used very flexibly for various purposes. The rotary tube furnace is slightly inclined and brought to the target temperature. The material is then fed continuously at the top of the pipe. It passes through the heated zone of the tube and falls out of the pipe at the lower end. The time of the heat treatment depends on the angle of inclination, the speed of rotation and the length of the working tube, as well as from the flow properties of the batch material. Equipped with the optionally available closed feeding system, the rotary tube furnace can also be used for processes in a defined atmosphere or in a vacuum. Depending on the process, batch and required maximum temperature, work tubes made of different materials are used.
Standard Equipment
- Tmax 1100 °C
- Working tube made of quartz glass open at both sides
- Thermocouple type N
- Tmax 1300 °C
- Open ceramic tube C 530
- Thermocouple type S
- Solid state relays provide for lownoise operation
- Heating elements on support tubes provide for free radiation
- Dual shell ventilated housing made of textured stainless steel sheets for low surface temperature and high stability
- Exclusive use of insulation materials without categorization according to EC Regulation No 1272/2008 (CLP). This explicitly means that alumino silicate wool, also known as “refractory ceramic fiber” (RCF), which is classified and possibly carcinogenic, is not used.
- Adjustable drive of approx. 0.5-20 rpm
- Digital display unit for the tilting angle of the rotary tube furnace
- Split-type furnace housing (opening temperature < 180 °C) provide for easy tube change
- Compact system, rotary tube furnace positioned on a base frame with
- Manual spindle drive with crank to set the tilting angle
- Switchgear and controls integrated
- Castors
- Defined application within the constraints of the operating instructions
- NTLog Basic for Nabertherm controller: recording of process data with USB-flash drive
- Controller with touch operation B500 (5 prgrams with each 4 segments)
Additional equipment
Additional Equipment
- Charge control with temperature measurement in the working tube
- Three-zone control for optimization of temperature uniformity
- Alternative work tubes for different process requirements
- Quartz glass batch reactors (Tmax 1100 °C)
- Higher temperatures up to 1500 °C available on request
- Vibrating channel on the rotary tube for convenient material supply, suitable for processes in air
- Powder discharge tube for easy material discharge, suitable for processes in air
- Feeding system for the continuous delivery of 5 liters of material under a defined atmosphere or vacuum, consisting of:
- Stainless steel funnel incl. electric vibration unit to optimize the material feeding into the working tube
- Electrically driven screw-conveyor at the inlet of the working tube with 10, 20 or 40 mm pitch and adjustable speed between 0.25 and 20 rpm
- Collecting bottle made of laboratory glass at the outlet of the working tube
- Gas supply package 26 for operation under non-flammable process gases (only in connection with the feeding system)
- Gas supply package 4 for hydrogen applications (only in connection with feeding system)
- Vacuum package for evacuating the working pipe, depending on the pump used up to 10−2 mbar
- Process control and documentation via VCD software package for monitoring, documentation and control
Technical specifications
Model | Tmax1 | Outer dimensions2 in mm | Max. outer | Heated | Length constant | Tube length | Max. | Electrical | Weight | |||
---|---|---|---|---|---|---|---|---|---|---|---|---|
tube Ø | length | Temperature1 +/− 5 K in mm | connected load | in | ||||||||
in °C | W | D | H | in mm | in mm | single zoned | three zoned | in mm | in kW | connection | kg | |
RSRC 80/500/11 | 1100 | 1770 | 1050 | 1310 | 80 | 500 | 170 | 250 | 1540 | 6.7 | 3-phase | 305 |
RSRC 80/750/11 | 1100 | 2020 | 1050 | 1360 | 80 | 750 | 250 | 375 | 1790 | 10.8 | 3-phase | 340 |
RSRC 120/500/11 | 1100 | 1770 | 1050 | 1310 | 110 | 500 | 170 | 250 | 1540 | 6.7 | 3-phase | 305 |
RSRC 120/750/11 | 1100 | 2020 | 1050 | 1360 | 110 | 750 | 250 | 375 | 1790 | 10.8 | 3-phase | 340 |
RSRC 120/1000/11 | 1100 | 2270 | 1050 | 1360 | 110 | 1000 | 330 | 500 | 2040 | 13.9 | 3-phase | 350 |
RSRC 80/500/13 | 1300 | 1770 | 1050 | 1310 | 80 | 500 | 170 | 250 | 1540 | 6.7 | 3-phase | 305 |
RSRC 80/750/13 | 1300 | 2020 | 1050 | 1360 | 80 | 750 | 250 | 375 | 1790 | 12.2 | 3-phase | 340 |
RSRC 120/500/13 | 1300 | 1770 | 1050 | 1310 | 110 | 500 | 170 | 250 | 1540 | 6.7 | 3-phase | 305 |
RSRC 120/750/13 | 1300 | 2020 | 1050 | 1360 | 110 | 750 | 250 | 375 | 1790 | 12.2 | 3-phase | 340 |
RSRC 120/1000/13 | 1300 | 2270 | 1050 | 1360 | 110 | 1000 | 330 | 500 | 2040 | 13.9 | 3-phase | 350 |
1Values outside the tube. Difference to temperature inside the tube up to + 50 K 2External dimensions vary when furnace is equipped with additional equipment. Dimensions on request. |
Request for quotation
Further products
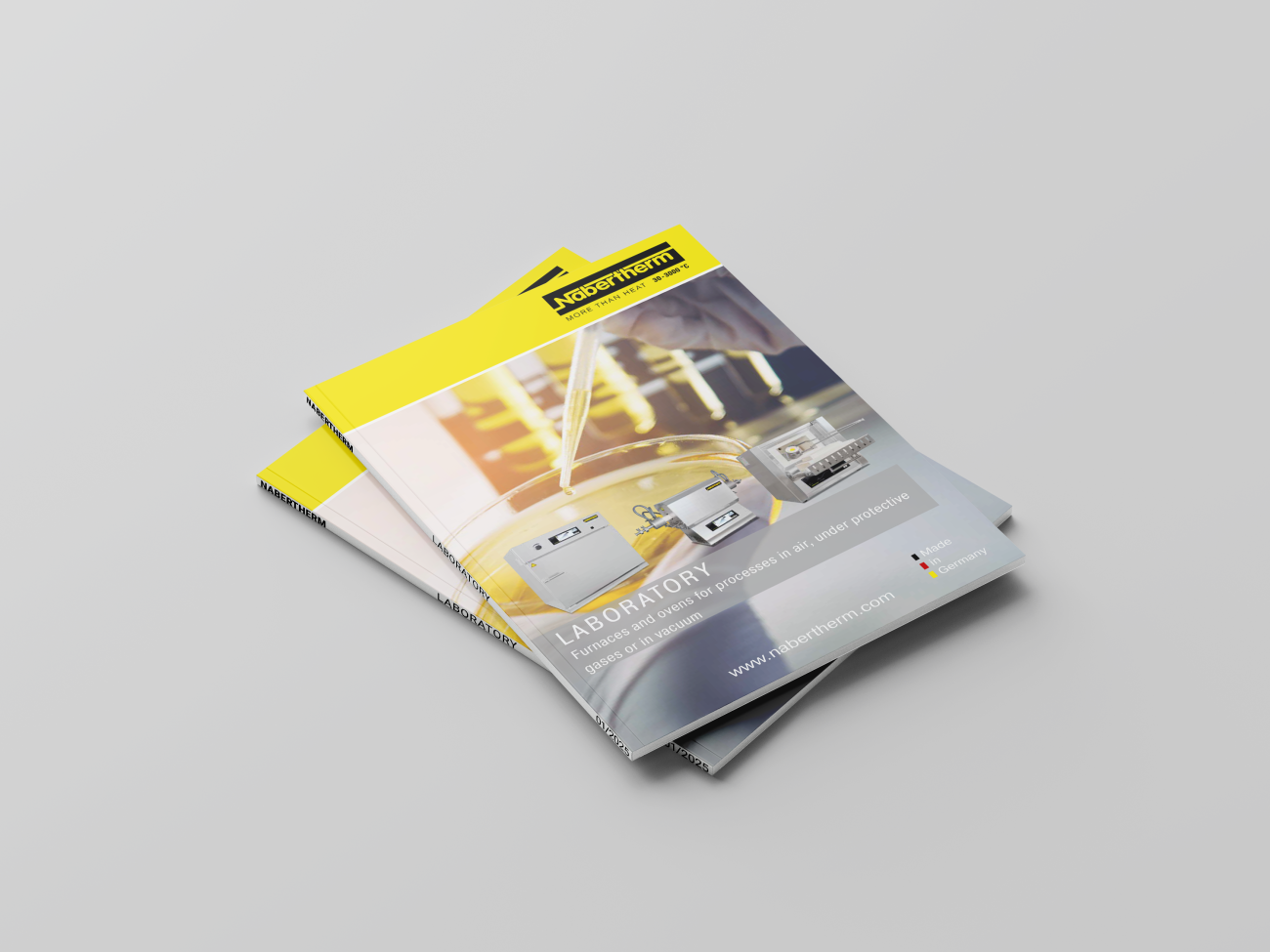
Catalog
A complete overview of our extensive range of furnaces, ovens and accessories for the laboratory can be found in our “Laboratory” catalog.